How 3D Printing Powers Full-Rocket Development at HyEnD
From early prototypes to launch-ready parts, the HyEnD student rocketry team uses the X1C to reduce costs, speed up iteration, and refine every subsystem.
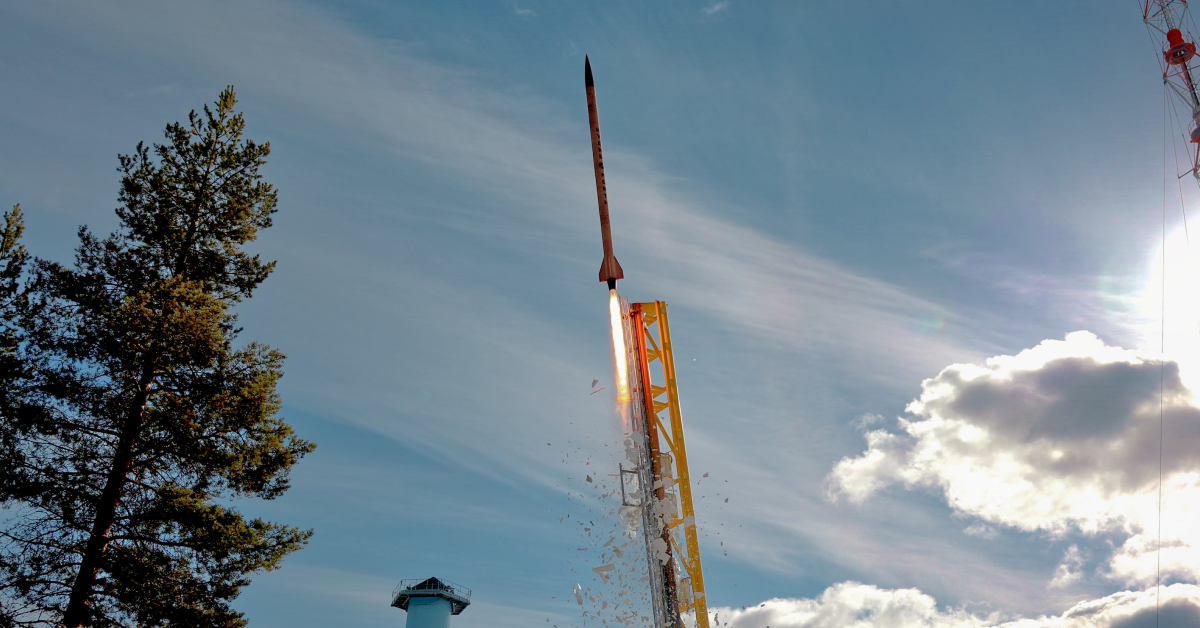
HyEnD is a student rocketry team from the University of Stuttgart that designs, builds, and launches advanced rockets.
In 2023, as part of the DLR’s STERN II program, they launched their hybrid sounding rocket N2ORTH to an altitude of 64.4km, setting new records for student-built and hybrid-propelled rockets.
Their current project, BLAST, is a 6-meter-tall, 300 mm-diameter liquid rocket developed to break world altitude records for student-built liquid rockets.
Most components are designed and manufactured in-house, with 3D printing playing a key role throughout.
“We really use 3D printing a lot, and our progress would not be possible without it.” – Ben Oker, Propulsion and Aerothermodynamics Engineer at HyEnD
Challenge: Diverse Manufacturing Needs on a Student Budget
Designing and building a rocket like BLAST means developing multiple subsystems – propulsion, structures, avionics, recovery, fluid systems, and ground support equipment (GSE) – each with its own components, requirements, and materials.
Many parts must be custom-made, fitted precisely, and tested under realistic constraints.
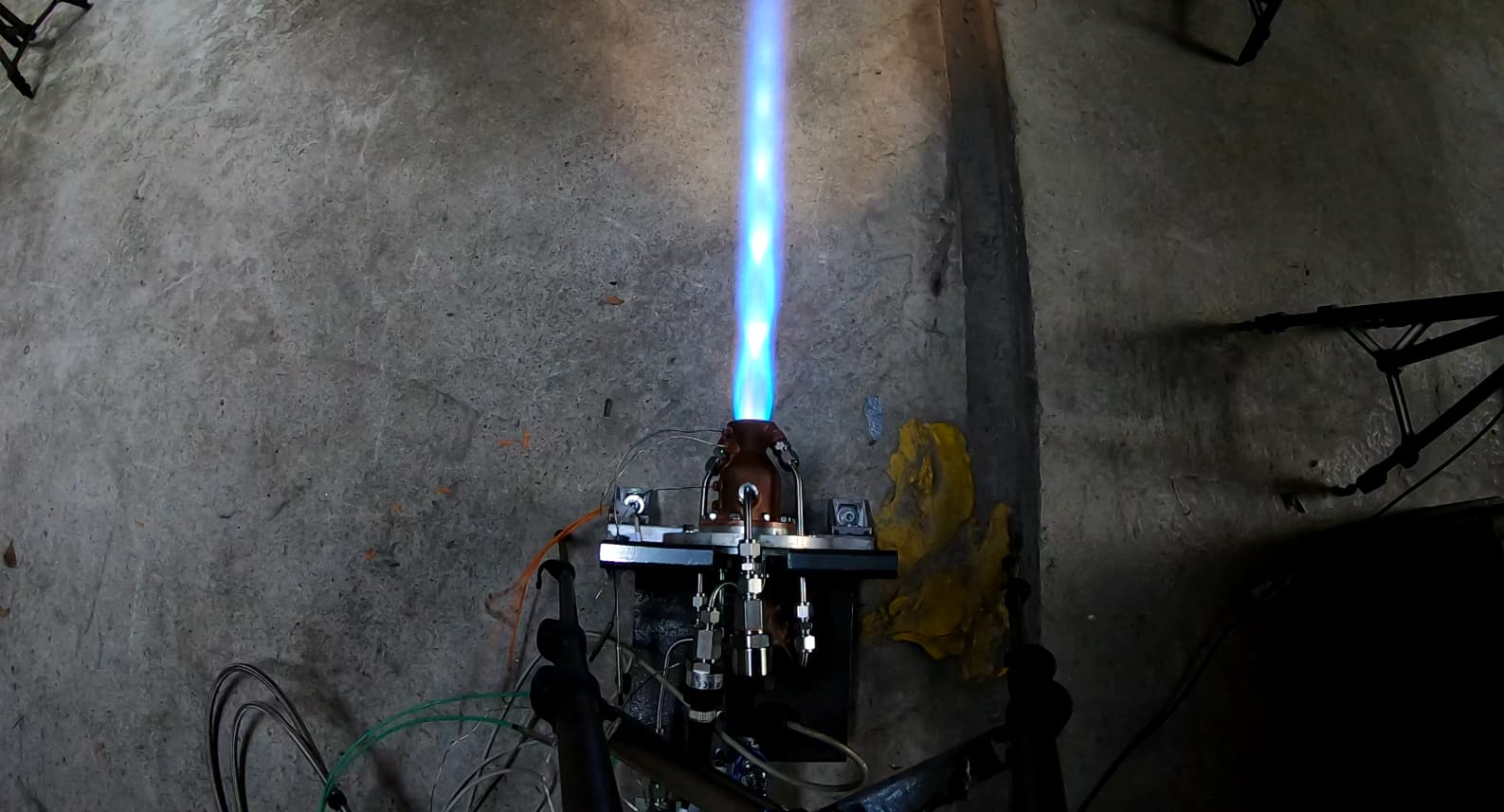
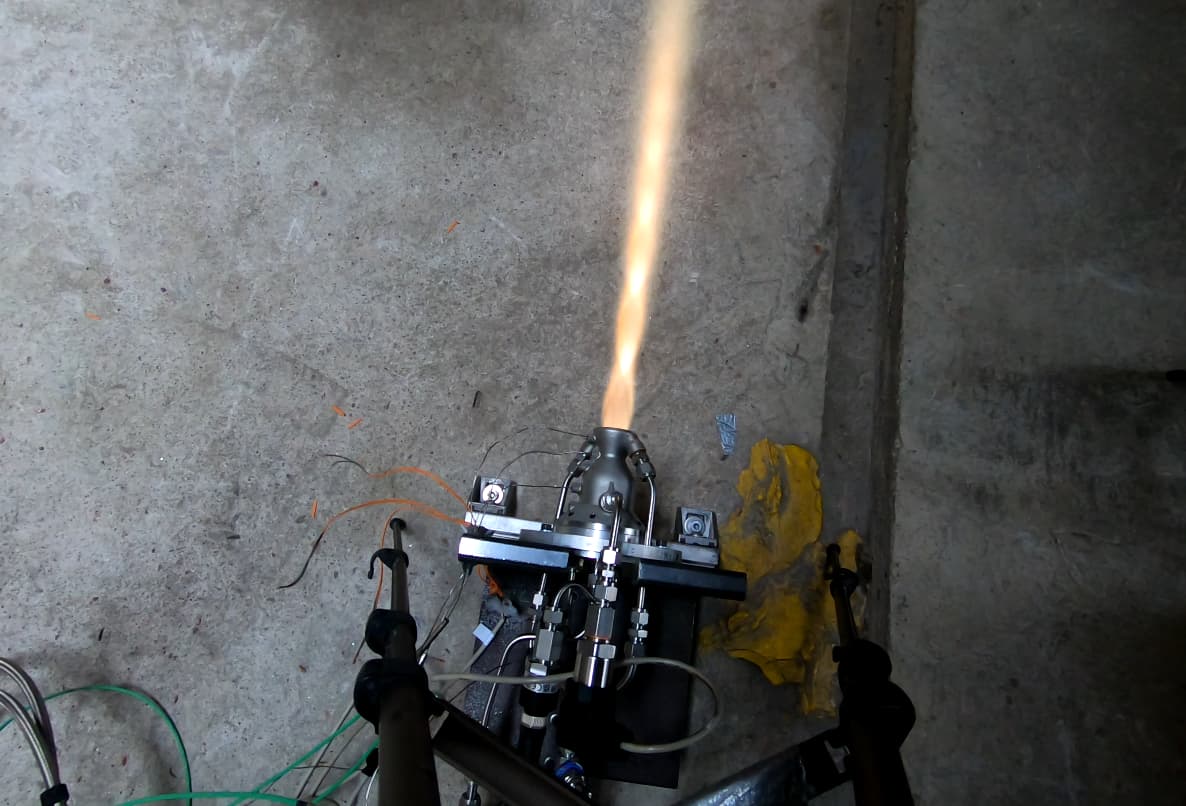
Example of engine testing. Left: Copper engine. Right: Steel engine.
Rapid iteration is essential, especially when final parts are costly to produce in metal. But traditional methods like CNC machining and manual fabrication are time-consuming, expensive, and difficult to scale across such a wide range of needs.
Solution: The X1 Carbon for Prototyping, Tooling, and Production
To handle constant design changes and a wide range of part requirements, HyEnD relies on a tool that fits seamlessly into every part of their workflow: the Bambu Lab X1 Carbon.
The team takes full advantage of the printer’s multi-material support and enclosed chamber, using around 4 kg of PLA per month and regularly printing in ASA, PETG, polycarbonate, and PVA depending on part function and environment.
Here’s how 3D printing fits into different parts of the rocket build:
Propulsion
- Engine component prototypes for visual inspection and sensor/piping clearance
- Fit-checks for complex assemblies prior to machining
- Custom jaws for holding metal parts during post-processing
- Sensor and valve mounts for high-pressure test bench setups
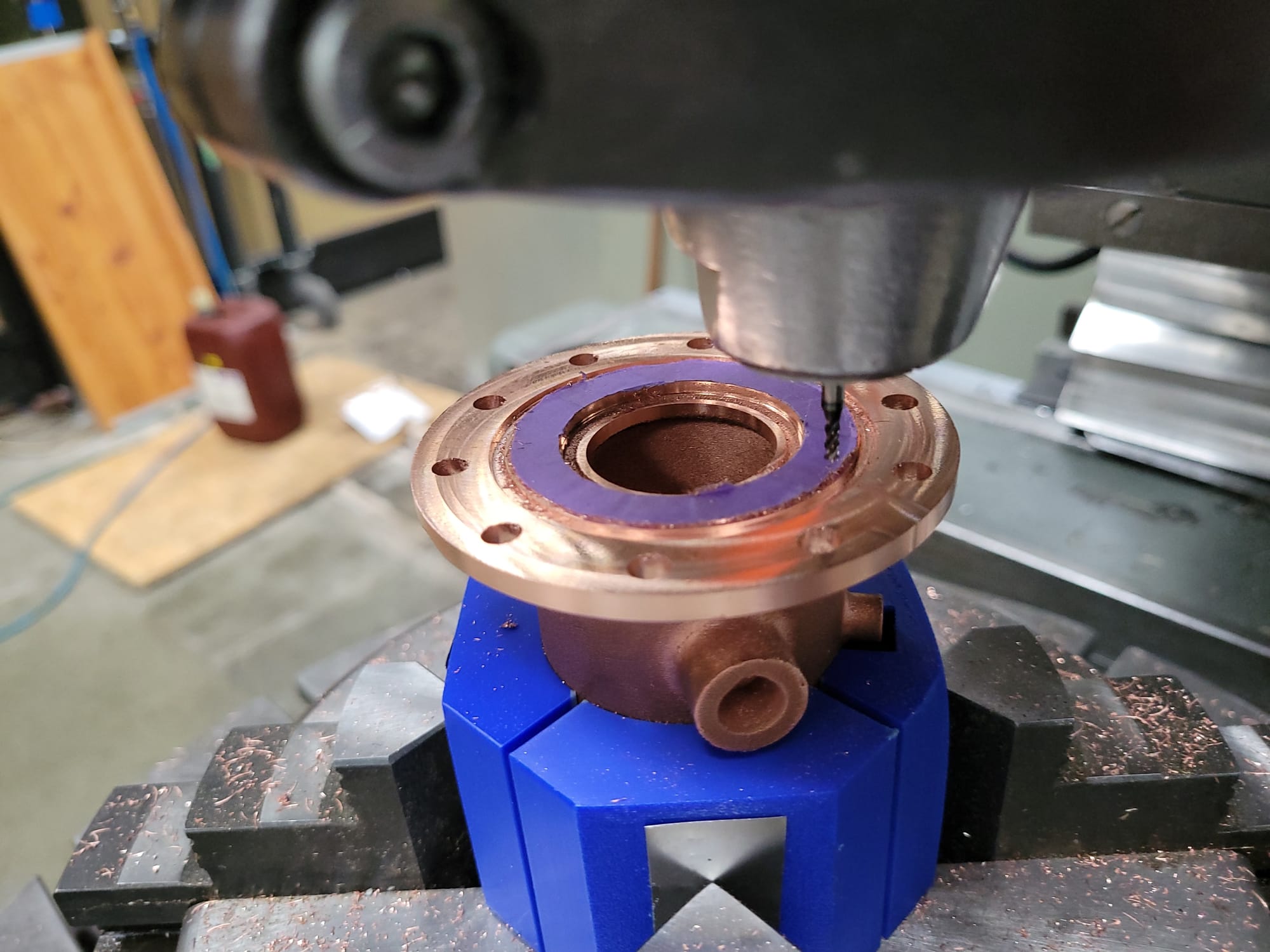
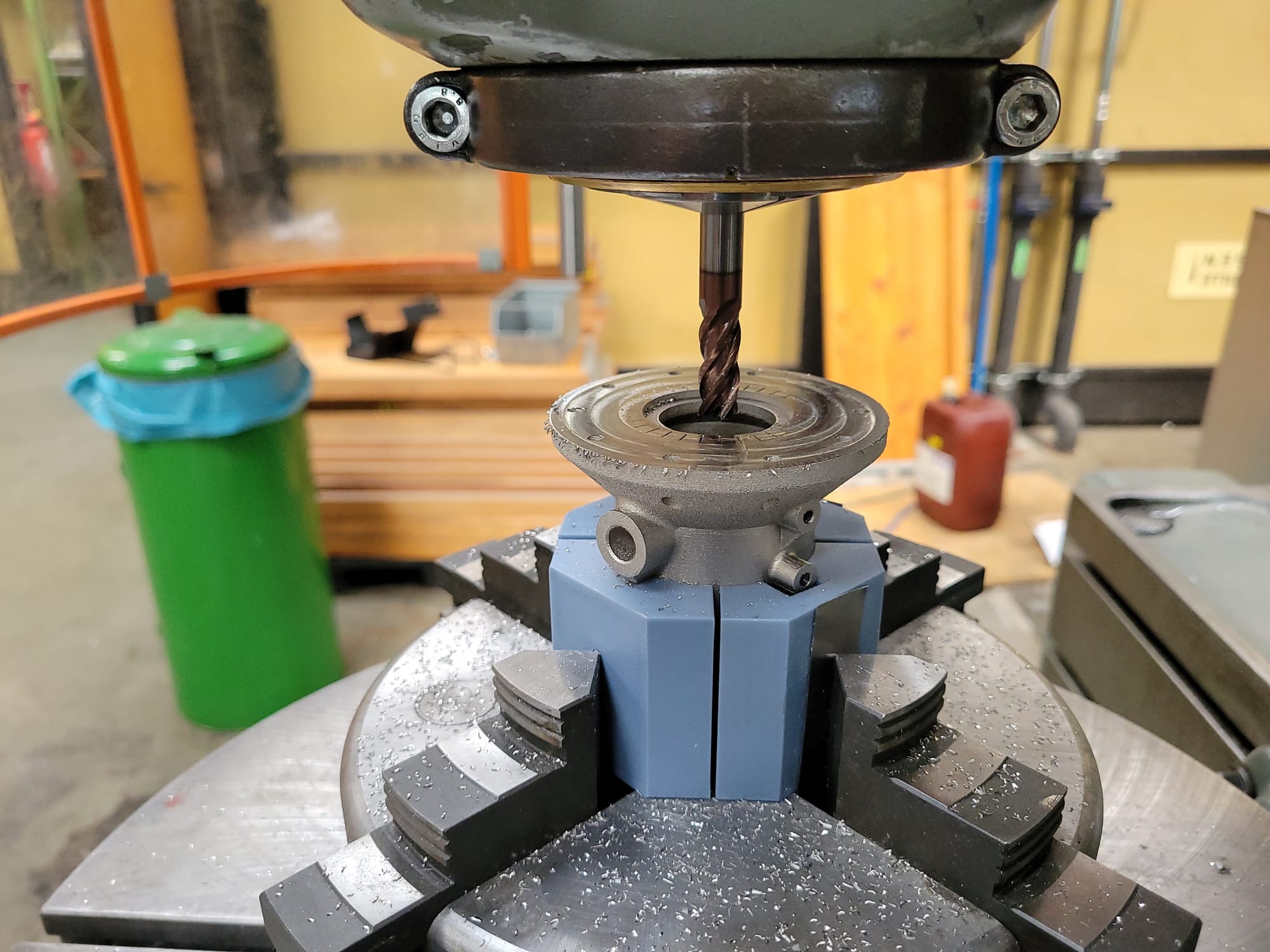
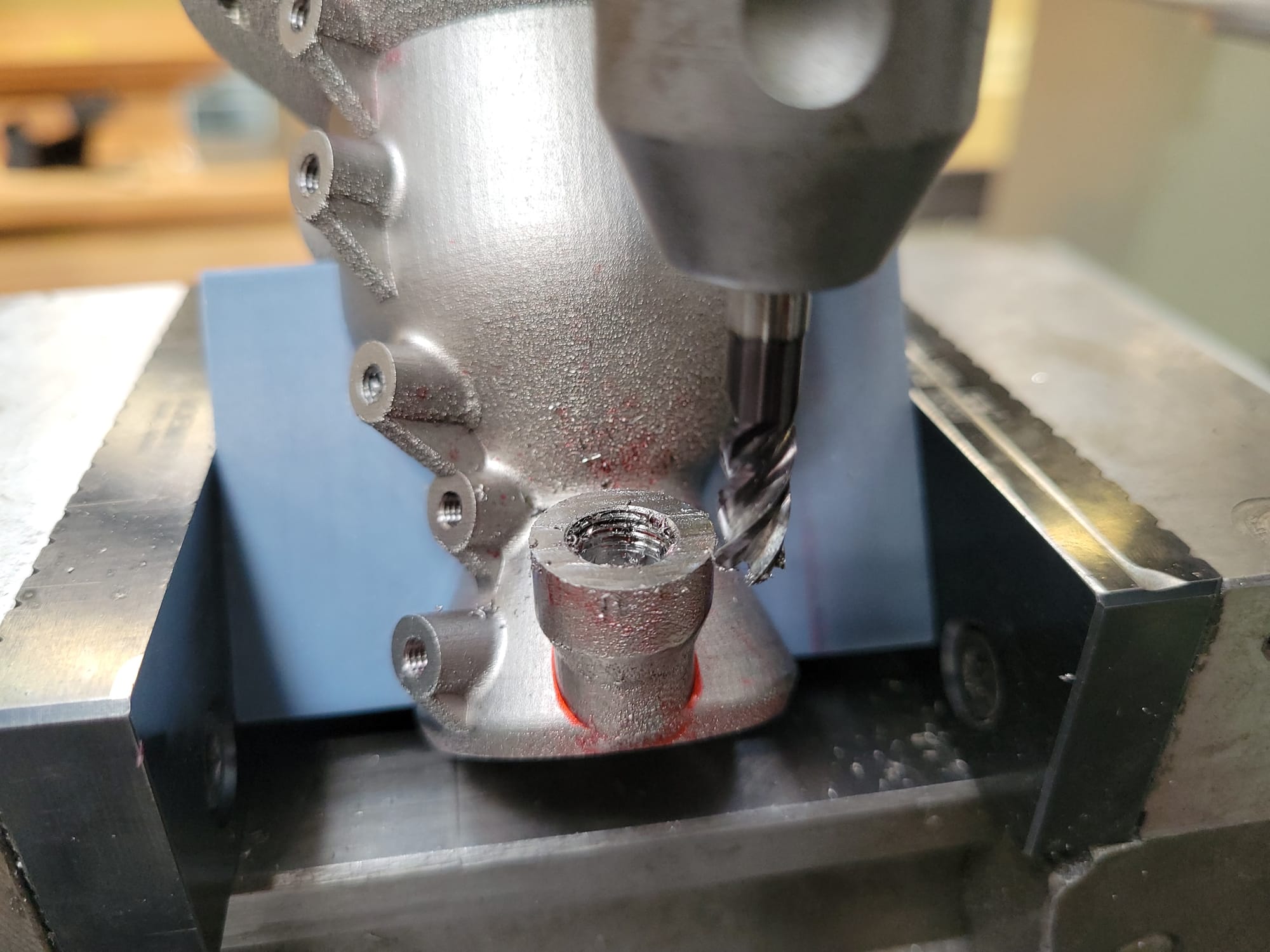
Examples of custom 3D printed jaws to CNC metal parts.
Ground Support Equipment (GSE)
- ASA brackets and mounts for outdoor use
- Protective housings for electronics and tubing
Composite Structures
- PLA and PETG molds for laying up carbon fiber structures
- PVA winding cores for filament-wound composite tanks, later dissolved to leave tanks rated for 200 bar
- Winding body prototypes for optimizing fiber paths
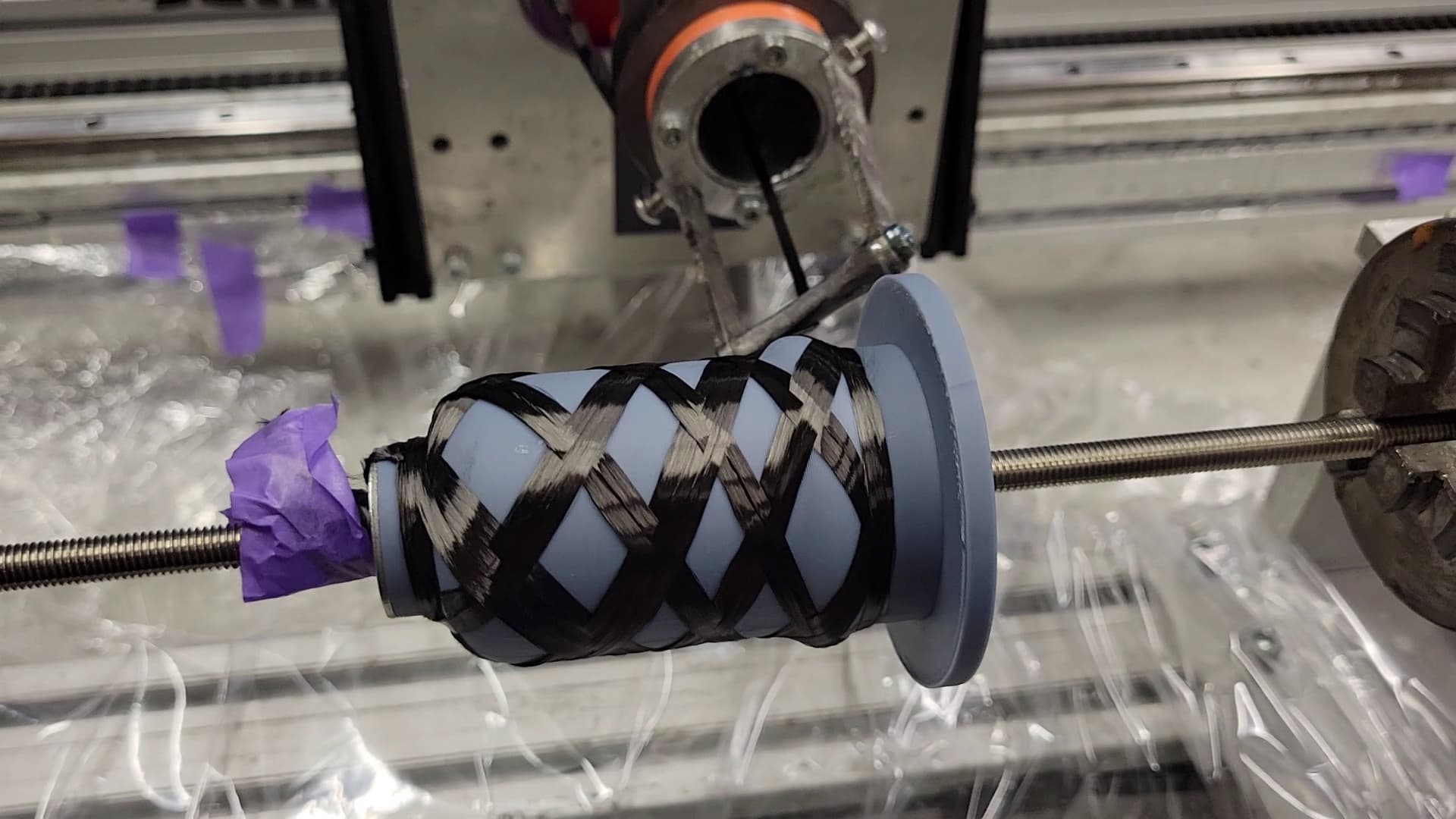
Recovery and Avionics
- Structural test parts for wind tunnel parachute trials
- Flight components like battery trays, sensor mounts, and PCB housings printed in polycarbonate or ASA
Fluid Systems
- Distribution block prototypes
- Pipe connector mockups to validate placement and integration
Want to see it all in action? The team recently tested their new liquid rocket engine:
Results: Rapid Iteration and Freedom to Experiment
The X1 Carbon helps HyEnD stay flexible and efficient as they develop and integrate parts across a highly customized rocket build.
It meets many of the team’s key needs:
- Supports fast, low-cost prototyping of complex components
- Enables quick fit checks and early testing before investing machining time and materials
- Manufactures functional parts with a variety of engineering-grade materials
- Allows custom tooling and fixtures to be produced in-house on demand
With faster turnaround and fewer bottlenecks, the team can experiment more freely and fine-tune every detail.
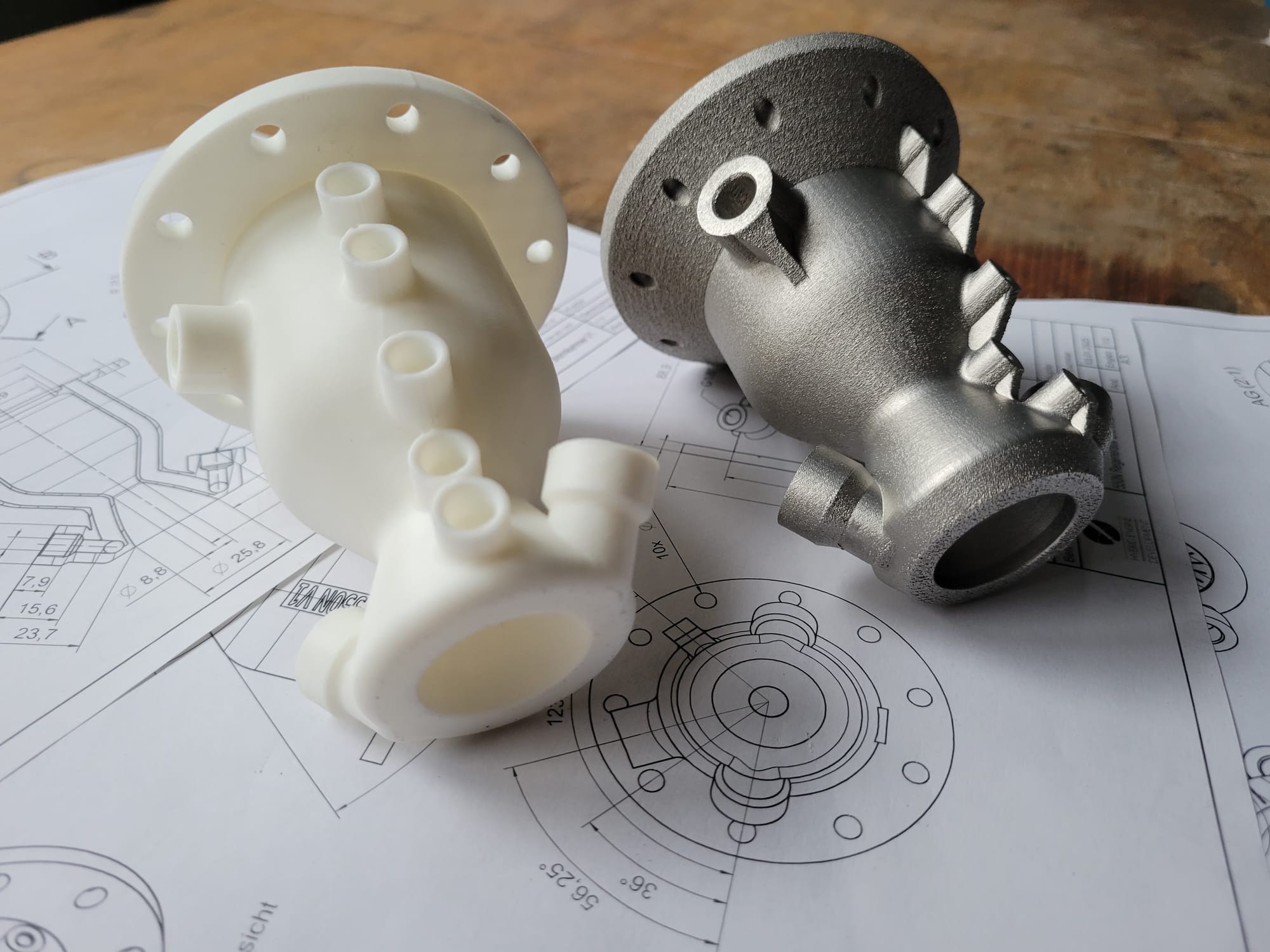
Looking Ahead: Supporting the Final Stages of Development
As the BLAST rocket takes shape, 3D printing continues to support the team through the final phases of development, from last-minute design changes to subsystem integration and test preparation.
The Bambu Lab X1 Carbon is a reliable part of their setup, helping them stay flexible, efficient, and focused on the next launch. Follow HyEnD on Instagram for more updates!
Want to learn more about how 3D printing supports advanced engineering projects like this one?
Explore more case studies from our community on the Bambu Lab blog or check out the X1 Carbon in detail.